Construction projects often face challenges like poor workability, weak adhesion, and fast drying. These problems can delay progress and raise costs. Thankfully, HPMC solves them with its amazing properties.
Hydroxypropyl Methylcellulose (HPMC) is a versatile additive used in construction to improve water retention, workability, adhesion, and consistency in materials like mortar, concrete, and tile adhesives. Its unique properties ensure high-quality, long-lasting results in various projects.
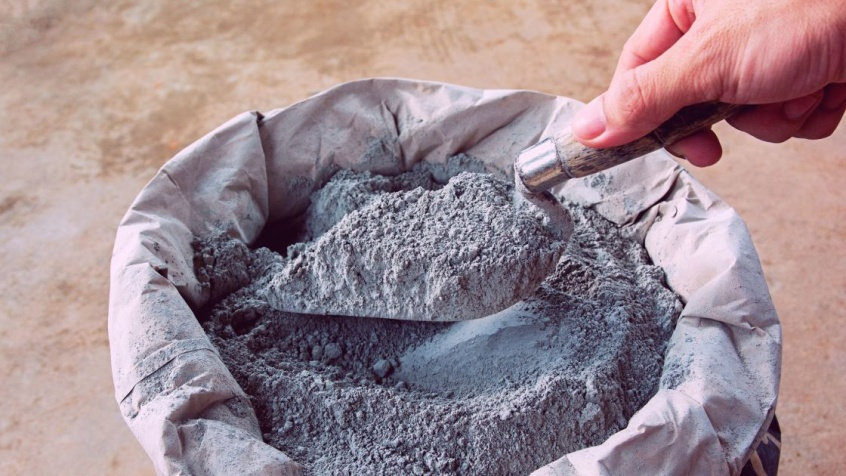
HPMC in construction
You know how the right materials can transform a construction job. I’ve seen HPMC make a huge difference for my clients at KEHAO. Curious about what it does and why it matters? Keep reading to find out.
What Is HPMC Used For in Construction?
Are you frustrated by materials that don’t stick or dry too fast? It’s a headache for any builder. I’ve learned HPMC can fix these issues and more.
In construction, HPMC is used to boost the performance of tile adhesives, plaster mortar, and gypsum plaster. It thickens mixtures, improves adhesion, enhances workability, and retains water for better, stronger results.
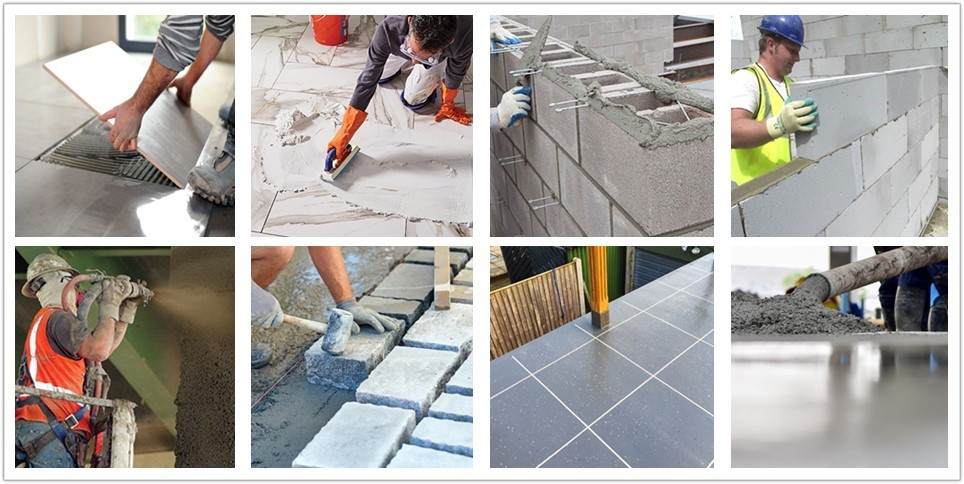
HPMC uses in construction
I love how HPMC works in so many ways. At KEHAO, we make it from natural cellulose, turning it into a powerful tool for construction. It shines in tile adhesives by thickening the mix and ensuring tiles stick tight, even in wet spots like bathrooms.
In plaster mortar, HPMC holds water so the mix cures right and stays strong. It also slows setting, giving you time to get the finish just right. Gypsum plaster gets the same perks—smooth surfaces with no cracks.
HPMC also helps self-leveling compounds stay even and avoid ingredient separation. In exterior insulation systems, it boosts durability against weather. Here’s a quick look at its roles:
Material | HPMC’s Job | Why It Helps |
---|---|---|
Tile Adhesive | Thickens, boosts adhesion | Strong bonds, more work time |
Plaster Mortar | Holds water, slows setting | Easier to work, less cracking |
Gypsum Plaster | Retains water, aids workability | Smooth finish, simple to apply |
Self-Leveling Compounds | Keeps mix consistent | Flat surfaces, no separation |
EIFS | Strengthens durability | Lasts longer, resists weather |
I once had a client in Thailand who couldn’t get tiles to stay put in humid conditions. After using our HPMC, their adhesives worked perfectly. It’s why I trust this product for any job.
What Are the Properties of HPMC?
Ever wonder what makes HPMC so special? Its standout traits tackle construction woes head-on. Knowing them helps me pick the best HPMC for my customers.
HPMC offers water solubility, thermal gelation, film-forming ability, and adjustable thickness. These traits make it a thickener, binder, and water retention agent in construction materials.
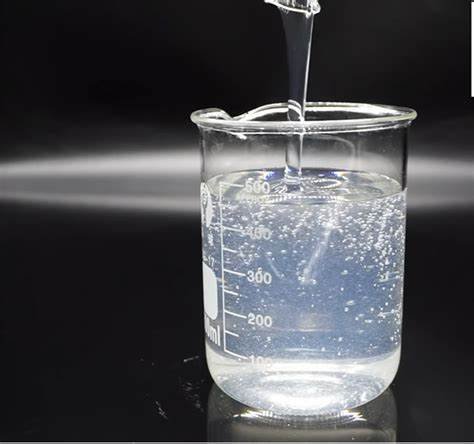
HPMC mixes easily with water, which I find perfect for mortar and concrete. When heated, it gels, controlling how the mix flows. This helps in places with changing temperatures.
It also forms a flexible film when dry. I see this as a shield in coatings and adhesives, adding strength. The best part? I can tweak its thickness. At KEHAO, we adjust it to fit any project.
Here’s how these properties help:
- Water Solubility: Blends smoothly into wet mixes.
- Thermal Gelation: Keeps mixes stable in heat.
- Film-Forming: Adds a tough layer for protection.
- Adjustable Thickness: Fits thick mortars or thin coatings.
For tiles, thicker HPMC stops sagging. For leveling compounds, a thinner mix flows better. My customer William from Colombia loves how our HPMC keeps his quality high and costs low. He says it’s a game-changer.
What Are the Applications of HPMC?
Not sure where HPMC fits in your projects? Its flexibility surprises me every time. Let’s check out its top uses.
HPMC is used in tile adhesives, plaster mortar, gypsum plaster, self-leveling compounds, and exterior insulation systems. It improves workability, adhesion, and durability across these materials.
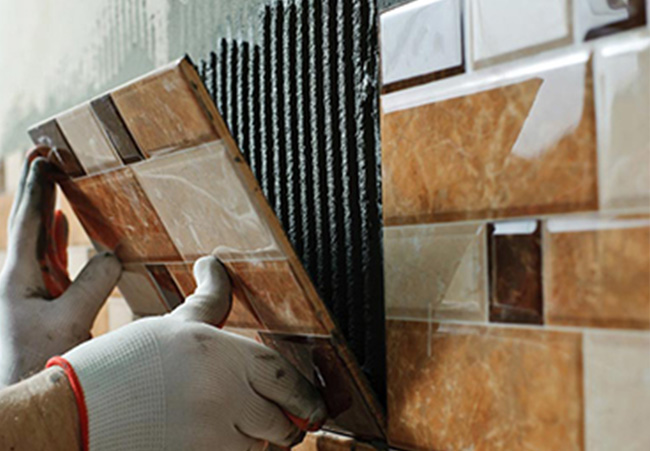
Applications of HPMC
I’ve seen HPMC shine in many jobs. In tile adhesives, it thickens the mix and sticks tiles firmly. It also gives extra time to adjust them. Plaster mortar gets better water retention and workability, making it easy to shape.
Gypsum plaster dries slower with HPMC, avoiding cracks and smoothing out nicely. Self-leveling compounds flow evenly and stay strong, thanks to it. Exterior insulation systems last longer with HPMC’s help against weather.
It doesn’t stop there. HPMC works in cement renders, masonry mortars, and joint compounds too. I adjust its amount to match each job’s needs at KEHAO.
A client in Africa told me our HPMC cut plaster cracking by 30%. Fewer fixes meant happier customers. That’s the kind of impact I aim for.
What Is the Use of HPMC in Concrete?
Curious how HPMC boosts concrete? It’s the backbone of big projects, and I’ve seen it struggle without help. HPMC steps in to fix that.
In concrete, HPMC improves workability, reduces water loss, and enhances mix quality. It retains water, ensuring proper curing and strength over time.
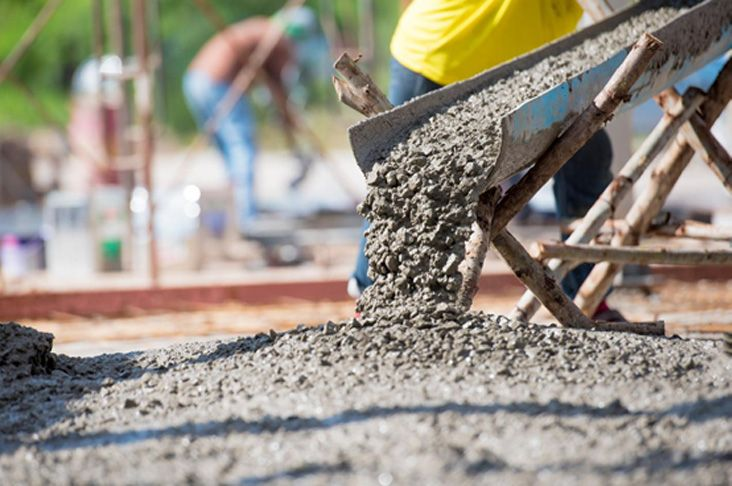
HPMC in concrete
Concrete needs the right balance to perform. I add HPMC to make it easier to pour and place, especially for tricky spots. It keeps water in, cutting down on cracks as it sets.
It also stops water from rising or aggregates from sinking. This keeps the mix even. Stronger, longer-lasting concrete is the result. Here’s a comparison:
Feature | No HPMC | With HPMC |
---|---|---|
Workability | Stiff or sloppy | Smooth and easy |
Water Loss | Dries out fast | Stays moist longer |
Cracking | More shrinkage cracks | Fewer cracks |
Strength | Uneven growth | Steady and strong |
HPMC isn’t as common in concrete as in mortar, but I love its effect in special mixes. A Southeast Asian client used it in a high-rise and got smoother, stronger results.
What Are the Benefits of HPMC?
Still doubting HPMC’s worth? I’ve seen it save time and money on-site. Let’s look at what it really offers.
The benefits of HPMC include better workability, stronger adhesion, improved water retention, and greater durability in construction materials. These lead to top-notch results and smoother workflows.
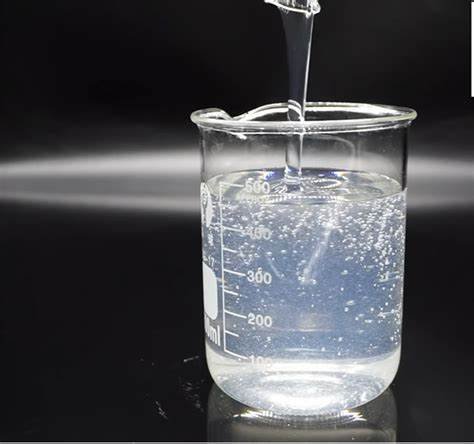
HPMC makes my job easier. It smooths out mixing and applying materials, saving effort. Adhesion gets a boost, keeping things like tiles stuck tight for years.
Water retention stops fast drying, so curing happens right. This means tougher finishes with less cracking. Quality stays steady, meeting tough standards every time.
It saves cash too. Less waste and fewer fixes cut costs. A Southeast Asian crew I supplied saw 20% less labor time with our HPMC in tile adhesives. That’s real value.
What Is HPMC for Drymix Mortar?
Wondering how HPMC fits into drymix mortar? It’s a go-to in construction, and I rely on it for great mixes.
HPMC in drymix mortar thickens, retains water, and improves workability. It ensures easy mixing, smooth application, and proper curing for strong, lasting results.
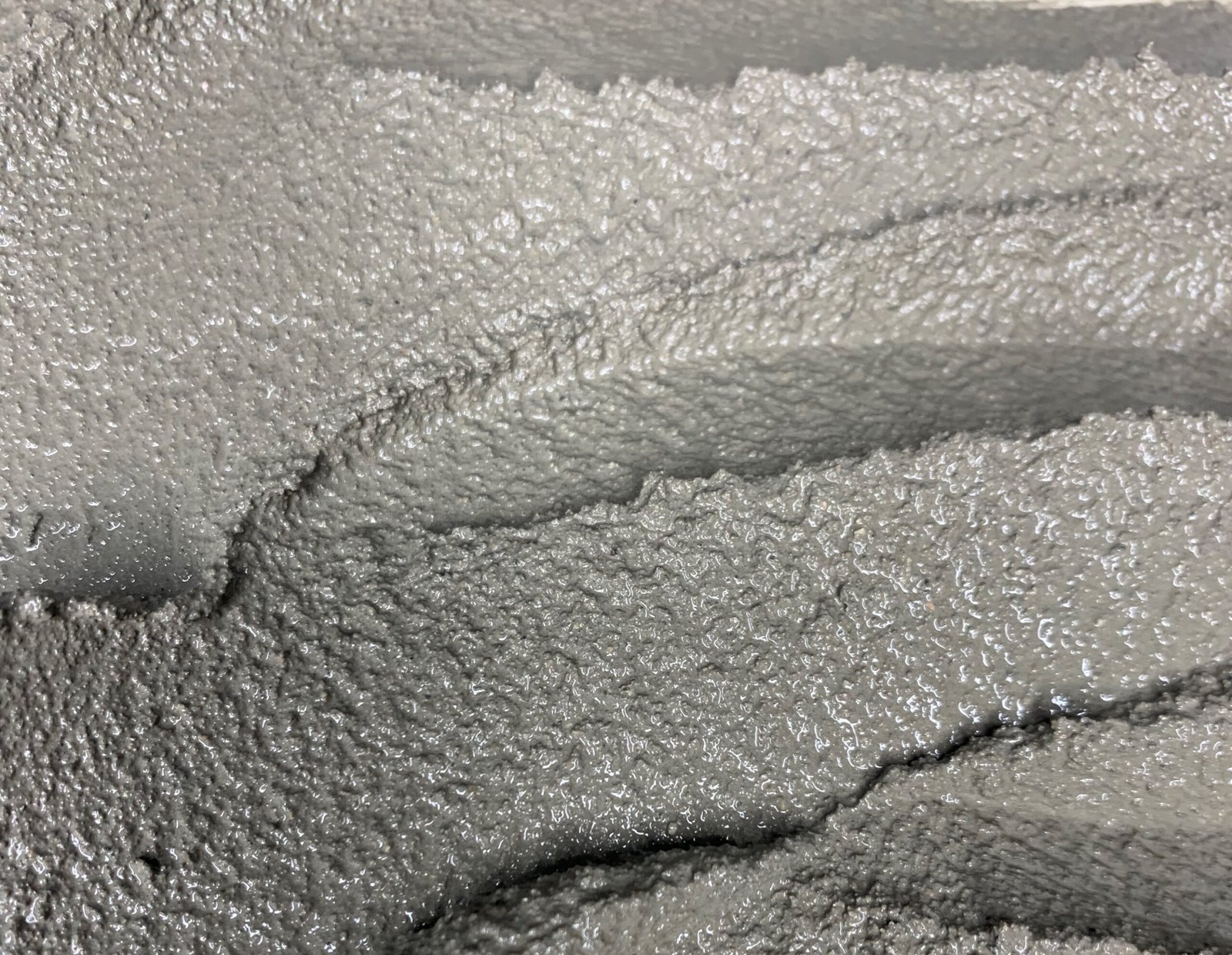
HPMC in drymix mortar
Drymix mortar is simple—just add water. I use HPMC to make it better. It thickens the mix, stopping sags on walls. Water stays in, letting cement set fully.
Workability improves, so spreading it is a breeze. Adhesion gets stronger, perfect for tiles or bricks. Here’s how it helps:
Mortar Type | HPMC’s Role | Benefits |
---|---|---|
Tile Adhesive | Thickens, sticks better | Firm hold, more adjust time |
Plaster Mortar | Holds water, aids workability | Easy use, fewer cracks |
Masonry Mortar | Retains water, bonds well | Stronger brickwork |
Repair Mortar | Thickens, adds strength | Lasts longer, fixes better |
I tweak HPMC for hot or cold climates at KEHAO. A European client cut costs 10% with our mix, boosting their sales. It’s a win for everyone.
Conclusion
HPMC is key in construction, offering water retention, thickening, and adhesion. I use it in adhesives, plaster, concrete, and drymix mortar for top results. It’s a must-have for quality work.